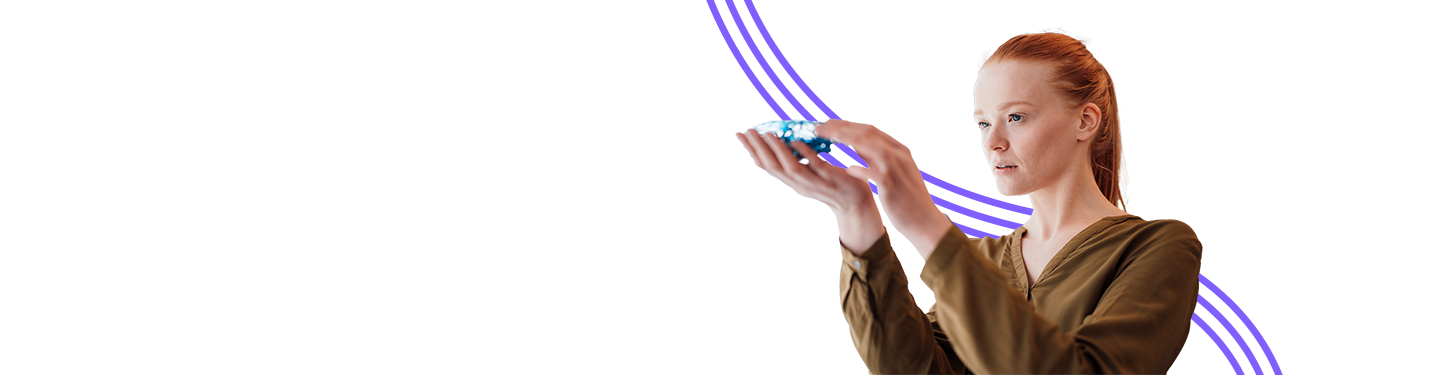
Case Study: Rapid Prototyping Additive Manufacturing Lab
Technology equipment leader reduces over 85% of time and expenses with on-site 3D printing for rapid prototyping
About the customer
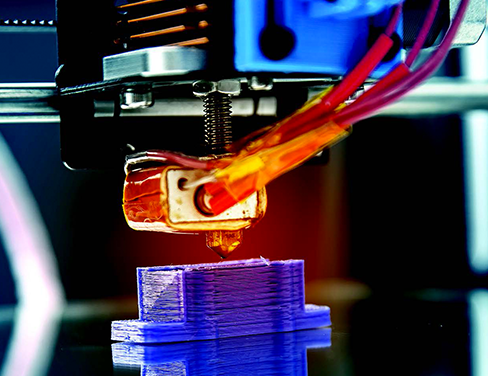
Headquartered on the West Coast, with dedicated customer operations and service centers worldwide, this leading equipment provider develops process control and yield management solutions.
In addition to enabling technology to support its engineering teams in their design, integration, and support objectives, the organization has incorporated additive manufacturing (AM) at many levels within the organization — including using AM for rapid prototyping purposes.
Serving the industry for over 40 years, the company has a portfolio of industry-standard products and a team of world-class engineers focused on design and integration.
“With its global presence already established within our company, we chose Ricoh to run the organization’s AM rapid prototyping lab and has successfully done so for over five years. Through our partnership, we continue to accelerate the AM infrastructure and service the company offers to its internal users.”
— Engineering Program Manager, AM Lab
Challenge
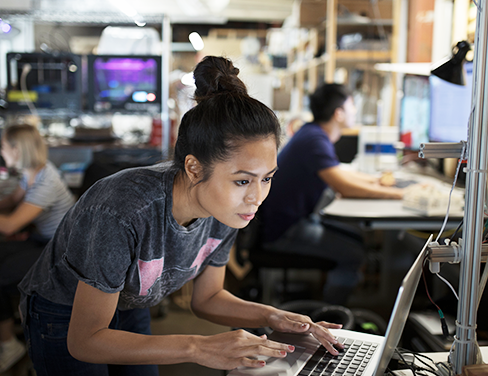
Increasing operational costs
Inefficient processing of print job requests
Inability to serve a significant number of internal users
Inadequate process control and tracking for on-site and outsourced requests
The company added 3D printing capabilities when it began using AM primarily for form and fit testing and, periodically, for function testing — depending on the material used. They also used AM for rapid tooling for R&D, production, service, and visual demonstrations for various technical and non-technical purposes.
Based on a 20+ year relationship with the organization, Ricoh became a trusted source for their traditional printing and managed services. Due to cost and delivery times, there was a recognized need for in-house 3D printing. Before bringing the printing on-site, the company would typically send a CAD/CAM file to an outside provider. The first model would arrive two weeks later. Engineers would review it and then — more often than not — send it back for modifications, adding another two weeks to the process, making it not only time-consuming but costly.
When they first ventured into 3D printing, there were many benefits. However, it took engineers and designers hours to produce a single prototype. Once complete, the prototype then needed to be cleaned and finished — adding time to the process and preventing them from focusing on their primary design engineering responsibilities. They outsourced the clean-up process, given the large volume of up to several hundred each month, which was also costly and time-consuming.
Moreover, the company wasn’t tracking print volumes or consumables used with various operators purchasing materials from the printer manufacturer that weren’t necessary for day-to-day production. While large prototypes needed to be outsourced, parts that could have been created on-site were outsourced due to lack of time from designers or inefficient processes — causing costs to rise.
Solution
“We have a knowledgeable partner in Ricoh, who staffs our rapid prototyping AM lab, and is closely integrated with our internal AM program team. Having Ricoh operating our 3D printing lab provides structure and quality as well as support and continued adoption for our employees and executives.”
— Engineering Program Manager, AM Lab
Integrated a specialized team to conduct assessment and recommend solutions
Extended current Managed Services agreement to cover 3D printing
Cut model time production by weeks to reduce costs by thousands of dollars
Brought costly outsourced services on-site
Dedicated a trained Ricoh team to the AM rapid prototyping lab
Created a simplified, streamlined and integrated tracking and billing tool
It didn’t take long for leadership to conclude that a centralized infrastructure was the best way to move forward, with dedicated resources to optimize job request and file processing, printing management, part post-processing, training and support to internal users.
The Ricoh Managed Services team, already on-site, began a conversation to understand and anticipate the company’s needs for its ongoing 3D printing program. Following an alignment with the company on their AM roadmap and objectives, Ricoh’s AM team assessed the printing environment and recommended addressing their specific challenges around ineffective operations and processes and increasing user adoption. One recommendation was implementing a rapid prototyping lab for the company’s engineers. Now, the lab contributes to the engineer’s expertise and has led to more efficient processes, such as creating CAD/CAM files needed by the Production Center.
Another recommendation was extending the existing copy, mail, and shipping managed services contract to cover AM rapid prototyping lab operations. Ricoh dedicated and cross-trained specialists to the ongoing management of the lab. Additionally, we standardized a process workflow for in-sourcing and outsourcing prototypes to make the best use of printers and resources — and track print jobs. We also created a single point of billing to simplify the internal cross-charging and outsourcing process and eliminated multiple purchase orders and individual credit card charges by the company’s users.
Results
More than 85-90% time and cost savings over traditional tooling
More than 15-30% time and cost savings overuse of external service bureaus
Savings of $500k to $1M in the first year by converting outsourced to in-house
Most jobs completed within 24 hours
More than 200% growth in usage of AM rapid prototyping
Today, the company has knowledgeable Ricoh staff alongside its internal AM program team to run its rapid prototyping AM lab. Having Ricoh experts operating the 3D printing lab provides structure and quality to a company-wide service and support for its employees and executives to adopt AM even further.
Ricoh’s presence instills confidence that each 3D printing job request will receive a proper review and the best recommendation for materials and AM technologies to use. Ricoh also manages the company’s user prototyping requests smoothly and effortlessly, usually requiring significant work from its users. The optimization of the AM rapid prototyping operation has led to time and cost savings of more than 85-90% over traditional tooling prototypes and more than 15-30% over the use of external service bureaus. Although Ricoh has established validated partnerships with external service bureaus to complement the needs in materials and technology that go beyond what it has internally, nearly 85% of prototypes are being cost-effectively printed in-house within 24 hours after receipt of the job request.
Overall, the success and adoption of the rapid prototype lab have exceeded the company’s expectations, and new opportunities are continually uncovered to increase efficiency and cost savings. By leveraging Ricoh’s operational efficiency and controls, the company can gain clear visibility into the benefits brought by AM rapid prototyping and establish better and faster strategic plans to meet the needs of the increasing footprint that AM has on its product and services.
Explore our All-In 3D Print solution or contact us to learn how fully managed on-site 3D printed prototypes can elevate your business.